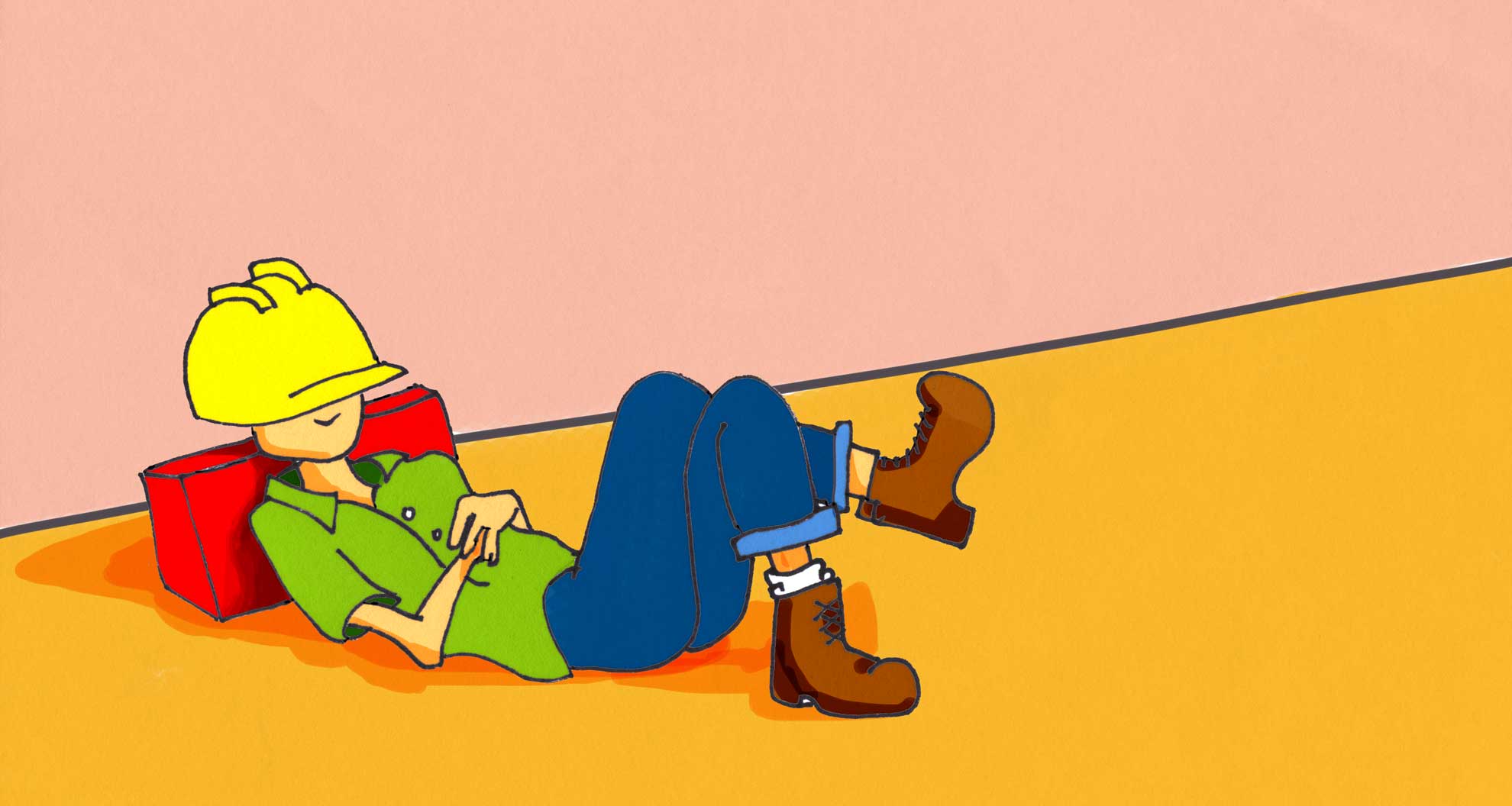
By Brandon Carrasco
Brandon Carrasco is the Director of Customer Solutions at Unirac, Inc. where he manages commercial project support and engineering services as well as field training. Brandon has also led new product development and managed products in residential, commercial, and utility solar segments.
I couldn’t believe that I was watching an installation crew member climb down the ladder for the 3rd time in an hour to grab some additional hardware, stop to grab a handful of Cheetos, and then climb back up on the roof. I wasn’t watching a crew from a no-name company. This was a serious regional installer.
A few weeks later I watched a different installation crew complete their second 6 kW residential install of the day by mid-afternoon. Multi-day installations were the exception, not the rule for this installer. They were synchronized and efficient.
A crew with a good process, combined with the right hardware, operates like a well-oiled machine. Waste is eliminated. The steps are repeatable which prevents errors. Each player knows their part, and everything comes together smoothly. DOWNTIME has been reduced.
What Is DOWNTIME?
DOWNTIME is an acronym used in Lean production. Each letter stands for one of the 8 types of waste that can be identified in any process. Use this list to find ways to eliminate waste in your installations and get a jump on the competition.
Defects – Catch Them in Process
Mistakes and incorrect installation can cost re-work time, extra material costs, and damage to customer property. Roof attachments are one example. Catching a problem with roof attachments during the installation of the remaining racking or modules can set you back significantly in terms of time and re-work. Check the first few and make sure the crew is installing them correctly. You may never fully eliminate defects, but you can implement a few ideas to greatly reduce them.
- Standardize roles and define the work standard for each
- Quality checks along the way
- Use simple tools like checklists
- Racking and other components should be easy to assemble (complexity and number of steps leaves room for error)
Overproduction – Don’t Trip Over Yourself
Have you ever seen a preparation or staging task over-done? Maybe a crew member stacks up too much material in the wrong location. This causes material piling up in the wrong areas and difficulty working around it. Follow these tips to keep this from becoming a problem.
- Don’t go overboard on “just-in-case” preparation work
- Have a plan to know when enough is enough
- Select racking and other components that need limited preparation work
Waiting – Balance the Work
No one likes to see crew members just standing around. Other crew members don’t like it, customers don’t like it, and your boss doesn’t like it!
- Balance workloads and roles
- Cross train newer installers to be more flexible
- Keep a stock of supplies on hand to prevent shortages
- Installers should plan ahead. When pilot holes are being drilled, flashings are not far behind. Once L-feet are installed, rails should be ready to mount. Using module level electronics? Can you do some pre-wire management of modules on the ground?
- Communicate with each other to keep things moving
Not-Utilizing Talent – Manage the Crew
Help your crew stay engaged. Everyone wants to feel like they are contributing.
- Fully train crew members
- Train them on work requirements and customer expectations
- Continue to cross-train newer installers
- Minimize any wasteful administrative tasks
Transportation – The Ups and Downs
Moving things around is a waste of time. This section is called “The Ups and Downs” because moving material up and down a ladder, or laddervator, should be limited to only what is absolutely necessary. Here are some other ways that you can minimize transportation waste.
- Ensure that materials are staged where they are needed
- Racking and other components should be packaged properly for your job type (kits, package quantities, and minimal packaging)
- Hardware and tools used across the jobsite should be carried in a toolbelt or pouch
- Minimize trips up and down ladders
- Certain pieces of hardware prone to rolling down the roof? Take a few extra to ensure that you don’t have to keep going down the ladder.
- Keep a stock of supplies on hand to prevent trips back to the warehouse or to a distributor
Inventory Excess – Take Only What You Need
Be careful with clutter on the truck or jobsite.
- Ensure that you have what you need, but not an excessive amount
- Don’t allow extra material to create trip hazards on the jobsite
Motion Waste – Go with the Flow
Get this right, and you are ahead of the game. Process flow will affect many of the other types of waste. This is the hardest to coordinate and requires team work.
- Understand how the system you are installing goes together ahead of time
- Select racking and other components that come pre-assembled and reduce the number of installation steps
- Think through the different steps
- Ensure that everything “flows” in the same direction
- Backtracking is a signal that there is wasted motion
- Communicate to not get in each other’s way
- Everyone should know their roles through the installation process. They should also know what steps need to be completed ahead of them, and what steps will be waiting on them.
Excess Processing – Standardize
Do you have to touch the same parts multiple times? Too many adjustments during and after installation? Those are signs that you are experiencing waste due to excess processing.
- Standardize and train how to do each step right the first time
- Install with racking designed to self-align or easily adjust without disassembly
- Choose racking and other components that require few, if any, tool changes
- Use the right tools and ensure settings are consistent
- Quality checks along the way (don’t wait until the end)
- Standardize how tools and inventory are loaded on each truck. Tape measures, wrenches, and other commonly-used tools should be in the same place on every truck. This is especially important for companies that have floating crew members, so they don’t waste time looking for common items.
Take Your Installs to the Next Level
Reducing waste in a process comes from consistent leadership. It takes commitment and time with crews to ingrain these tips into your everyday workflow. Lean principles have made dramatic improvements in manufacturing productivity and quality over the past few decades. Apply lean principles to your installation business and you can see dramatic increases in profitability and quality. Your efforts combined with the right products and manufacturer’s support teams will help take your team to the next level.
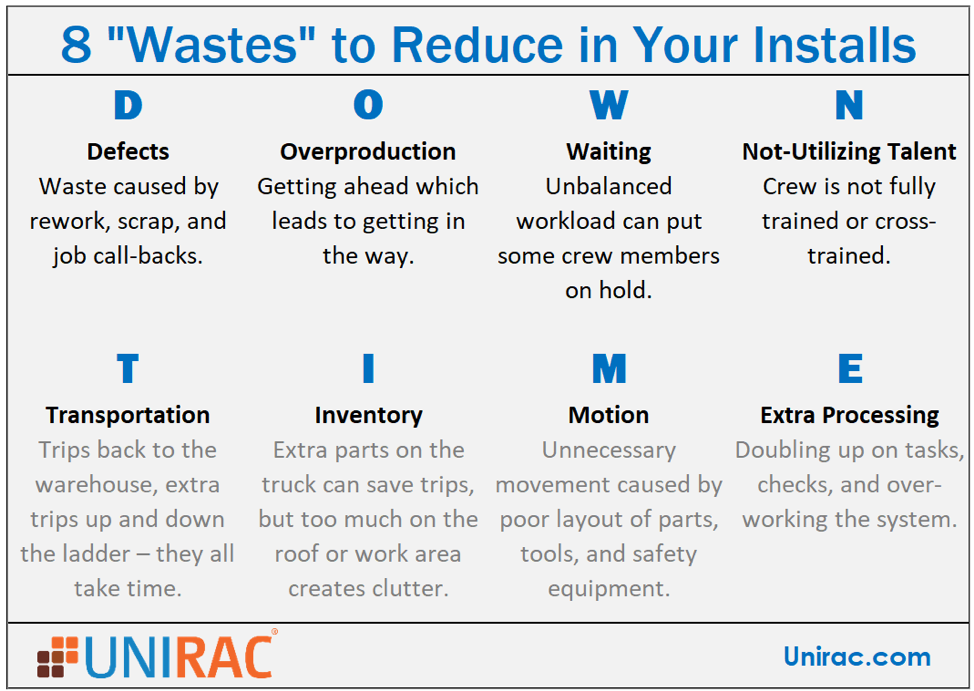
This tip was contributed by Brandon Carrasco, Director of Customer Solutions for Unirac.