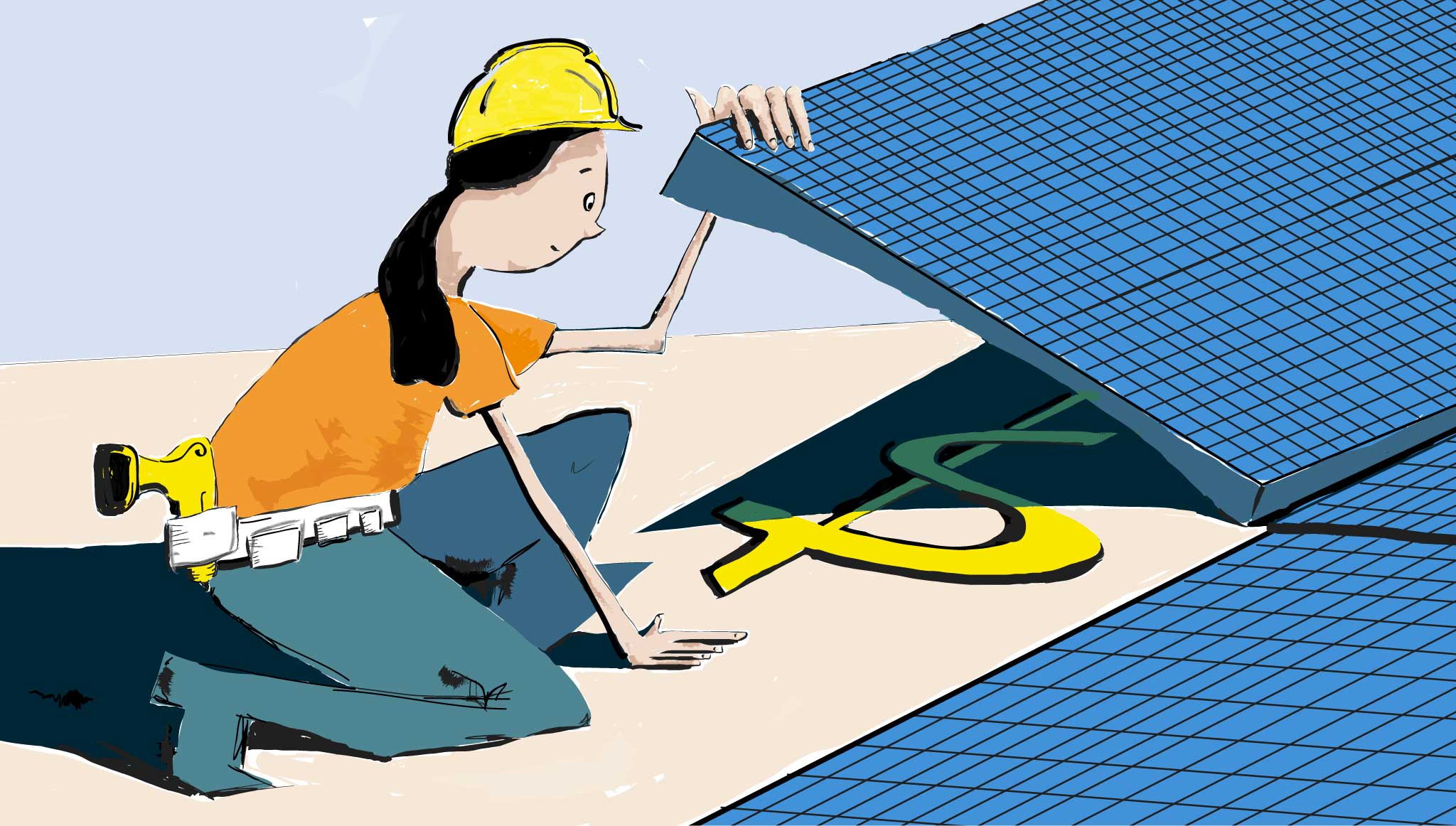
Predictions of a flat year for residential solar in 2018 means reduced sales for many solar contractors. A key to maintaining company profitability in a flat year is managing costs. Reducing installation time and increasing installation accuracy are some things in your control to surface unrealized cost savings.
Labor Cost Trends
At a macro level, studies indicate that installation labor costs have decreased over time. In 2012, a Rocky Mountain Institute report on rooftop solar costs in the U.S. pegged installation labor at about 50 cents per Watt. By 2017, when the National Renewable Energy Laboratory released its latest benchmark for solar installation costs, labor for residential projects had fallen to 30 cents per Watt. Yet German companies long ago trimmed their labor costs to less than 20 cents per Watt. Achieving this benchmark requires a more in-depth look at what additional waste can be eliminated or minimized.
Time Is Money
If you are merely tracking salaries to define your labor costs, you are missing the opportunity that lies with having a sound methodology to measure and improve “installation efficiency.” Lowering labor costs should not come from compromising on safety, quality, or employee compensation. Your attention should be on how to benchmark what your crews are currently doing and identifying the ways that creating and standardizing processes could save time (which of course translates into saving money).
Here are three steps we recommend to tackle this at your company:
-
Document installation tasks
Rooftop solar installations, like all projects, can be broken down into their component parts. You load equipment and supplies into a work vehicle and unload them at the job site. You may locate attachment points for roof penetrations before installing a mounting system. There are electrical wiring and conduit and grounding for the electrical system and metal parts. The major components—modules, inverters, and mounting systems—all come with step-by-step instructions for the install crew.
Part of the contractor’s job is to source equipment that minimizes unnecessary and time-consuming steps in the installation process. When evaluating a new product, talk to the supplier about estimated installation times. Watch a demonstration, if possible. And consider how well your crew members will be able to repeat the process. Sometimes it’s worth paying a higher price for a product that saves time. Time savings not only reduce your labor costs, but they also add value for your customers who want the job done right and want you off their roof and out of their driveway as quickly as possible.
-
Track time
Once you’ve documented installation tasks, use this information as a tool to monitor consistency and seek out opportunities for improvement. Look at how companies with a remote workforce, including construction contractors, are using mobile time tracking software like ClockShark and busybusy to increase visibility into labor costs. At a basic level, they provide paperless time sheets and real-time job costing updates. If you train employees to log key tasks in the installation process and incentivize them to do so, you can begin to evaluate the effectiveness of your installation process, the ability of your system components to save time, and the consistency of your technician team. Ask the software provider if its time tracking program integrates with your accounting program to minimize time spent on manual data entry when you go to analyze the results.
-
Analyze results
Enphase Energy has produced an e-book called the Solar Survival Guide, showing its installers how to streamline various aspects of their business. In the chapter about team efficiency on the job site, Enphase shared a template for documenting variables that influence efficiency, including details about the project, the crew, system components, and the building structure. Consider these variables when you analyze results, which you should do on a regular, ongoing basis.
Once your dataset reaches a meaningful sample size, try to understand the conditions that optimize labor efficiency. Do installations take less time in one permitting jurisdiction or another? How do weather conditions affect installation efficiency? If you have installed more than one set of modules, inverters, and mounting systems, which components deliver the most time savings?
By taking time to benchmark and standardize your installation processes, you can identify and implement improvements that drive down your labor costs and build a healthy, profitable company. What is your company doing to measure and improve installation efficiency?